What Are The Main Defrosting Methods in Refrigeration?
There are five main defrosting methods used in cold rooms and freezer rooms.
- Off cycle defrost
- Electric defrost
- Water spray defrost
- Hot-gas bypass defrost
- Reverse cycle defrost

Air cooler evaporator and outdoor condensing unit are two major components of the cold room and freezer room. The outdoor condensing unit is installed outside of the cold room or building, so it is also called remote condensing unit or cold room outdoor unit. The evaporator is installed inside of the cold room, so it is also called cold room indoor unit. They composed of cold room refrigeration system.
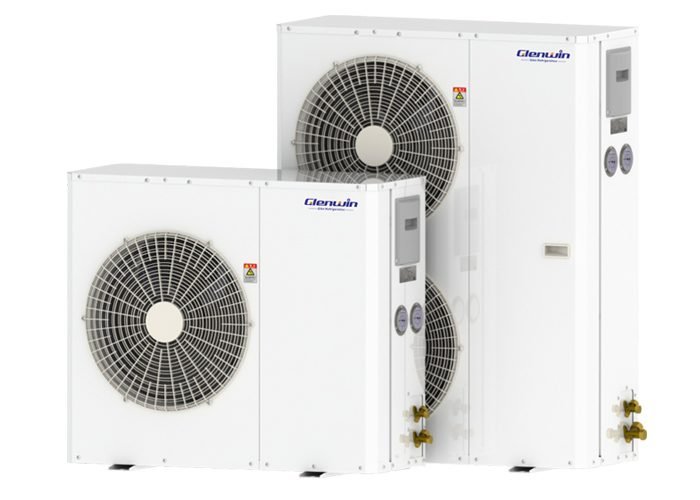
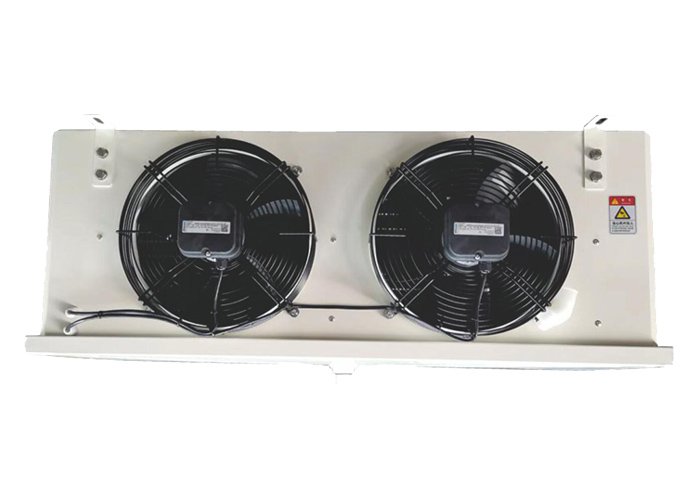
The cold room evaporator has the advantages:
- High heat exchange efficiency
- Compact structure
- Strong air supply
- Good cooling performance
- Easy to control the defrost
- Easy to control and operate
- High reliability, not easy to leak
- Low initial investment
Due to these advantages, the evaporators are widely used in different kinds of cold rooms and freezer rooms and has become the most commonly used evaporator in cold storage.
According to different applications, there are three main types of cold room:
Type of cold room | Temperature | Application |
Chiller room | -5°C~5°C | Keep the food fresh suck like fruit cold storage, vegetable cold storage, milk cold storage, fresh meat cold storage, egg cold storage, flower cold storage and much more. |
Freezer room | -10°C~-20°C | Keeping the food in in frozen state, like seafood cold storage, meat cold storage and much more. |
Blast freezer room | -20°C~-35°C | Blast freeze the fresh fish, fresh meat and also reserve the ice-cream and chemicals at low temperature. |
When the surface temperature of the evaporator is lower than 0°C, the moisture in the air will frost or freeze on the surface of the evaporator coil. Those frost or ice will prevent the refrigerant in the system from absorbing heat inside the cold room. Especially in freezer room and blast freezer room, it is easy to frost.
The thermal conductivity of copper is 397W/m.K, and the thermal conductivity of frost is only 0.116~0.139W/m.K. Moreover, the frost layer will narrow the air flow channel, reduce the air volume, and eventually completely block the evaporator. Excessive frost layer will worsen the working conditions of the refrigeration system, making it difficult to cool down the cold room, reducing the cooling capacity of the compressor, and increasing its power consumption. Therefore, the evaporator in the cold storage needs to be defrosted every 5 to 8 hours operation.
What Is Off Cycle Defrosting Methods In Refrigeration?
The off-cycle defrost is one of the most simplest defrost methods in refrigeration. This method turns the refrigeration system off and naturally let the frost or ice melt off the coil by the normal air. When the system turns off or pumps down, the evaporator fans keep running, which forces the system to defrost.
The off-cycle defrost widely used in high-temperature refrigerated display cabinets. It is controlled by a time controller. When the defrost time is reached, the defrost time controller automatically stops the compressor. The heat emitted from the food in the cabinet melts the frost layer attached to the surface of the evaporator. When the defrost time is end, the time controller automatically starts the compressor and terminates the defrost.

What Is Electric Defrosting Methods In Refrigeration?
Electric defrost is one of the most common defrosting methods in refrigeration. It uses electric heating tube to melt the frost layer. The electric heating tubes are installed between the evaporator coils and also be placed in the water tray. In order to melt the frost as quickly as possible, the power of the electric heating tube can’t be choose too small, usually several thousand watts. Generally the electric defrost cycle is every 4 hours to 8 hours (need to set according to the actual situation). The operation of the electric defrost heater generally adopts refrigeration defrost timer to control.


What’s The Advantages and Disadvantages of Electric Defrost System?
Now most of the cold rooms and freezer rooms adopts electric defrost refrigeration system. Compared with hot gas defrost, electric defrosting is a convenient defrosting methods in refrigeration.
Advantages of electric defrosting:
- Simple refrigeration defrost cycle
- Easy and convenient to operate
- Low initial investment
Disadvantages of electric defrosting:
- Consumes too much power
- Not energy-saving
The electric defrost method has simple refrigeration defrost cycle and is easy and more convenient to operate. However, each square meter of heat exchange area of the cold room evaporator is equipped with approximately 40~100W electric heating tubes, which consumes too much power and has a great impact on the fluctuation of the storage temperature. It is not energy-saving. The refrigeration defrost heaters are very powerful. If the quality of the electric defrost heater is not good or it has been used for a long time, it is easy to burn out or even cause a fire. Electric heating defrost poses serious safety risks.
The freezer defrost cycle temperature and defrost timer settings are very important. During the use of the cold storage, you will find that sometimes the frost in the cold storage has finished melting, but defrost is still going on; and sometimes cooling has started, but the frost has not finished melting. This means that the defrost time or the defrost temperature has been improperly adjusted and needs to be readjusted. We suggest out customer to defrost every 4 hours to 8 hours, but need to adjust according to the actual situation.
The walk in freezer evaporator is one of the most important components in refrigeration system. How to install a TXV? How to set the freezer defrost cycle temperature? These are the keys to using a good evaporator. In order to help our customer use our evaporators well, we provide a “TXV Installation Recommendations”.
Please download “TXV Installation Recommendations” or click here for more details.

On the “TXV Installation Recommendations”, there is our suggestion for electric defrosting:
Defrosting Interval: 4~8 hours (according to the frosting situation)
Stop Defrosting Temp.: 15~18℃ (Defrost probe temp.)
Drip Time: more than 5 minutes
What Is Defrost Drip Time?
After finishing the defrost, there is a water drip down time. The drip down time means a short period of time that will allow melted frost to drip off the evaporator. It is better to set more than 5 minutes for drain. It is especially critical in low temperature freezer room.
What Is Water Spray Defrosting Methods In Refrigeration?
Water spray is an efficient defrosting methods in refrigeration. It is a refrigeration defrost method that uses a water pump or water spray device to spray water on the outer surface of the evaporator, so that the frost layer is melted and washed away by the heat of water.
What’s The Advantages and Disadvantages of Water Spray defrosting in refrigeration system?
Water Spray defrost is an efficient defrosting methods in refrigeration, it has the advantages below:
- Simple operation and short time
- A effective defrost method
- Small storage temperature fluctuation
Disadvantages of electric defrost:
- More water wastage
Water spray defrost method has the advantages of simple operation and short time, but it needs a lot of water, and the water temperature should not be lower than 15°C, so in lower ambient temperature areas, it is not suitable to use water spray defrost due to the low water temperature.
What Is Hot-gas Bypass Defrosting Methods In Refrigeration?
Hot gas bypass defrost is one kind of hot gas defrost methods in refrigeration. It uses the hot gas defrost piping (a bypass line) and on-off solenoid valve to allow the high-temperature refrigerant to flow out from the compressor to the evaporator directly. In hot gas bypass defrost technology, the high-temperature high-pressure gas discharged from the compressor flows directly to the evaporator through the bypass line and use the heat to defrost. Hot-gas bypass defrost uses gas to defrost, but without changing the refrigerant flow direction.

What’s The Advantages and Disadvantages of Hot-gas Bypass Defrost?
Advantages of hot-gas bypass defrost:
When use this defrosting method in refrigeration system, it don’t need the four-way valve, the hot gas defrost valve (solenoid valve) is opened, the fan is turned off, and the compressor discharges high-temperature gas passes through the bypass pipe to the evaporator for heat release defrosting.
Disadvantages of hot-gas bypass defrost:
The energy for hot gas bypass defrosting still comes from the compressor. The energy loss during the defrosting process is large, and the defrosting time is longer than that of the reverse cycle defrost.
What Is Reverse Cycle Defrosting Methods In Refrigeration?
Reserve cycle defrost is also one kind of hot gas defrosting method, but it is different from the hot gas bypass defrost. They both need the gas to defrost, but reserve cycle defrost uses 4 way solenoid valve operation to change the refrigerant flow direction, while the hot gas bypass defrost don’t change the refrigerant flow direction.
How Does A Hot Gas Defrost System Work?
The hot gas defrost cycle is the opposite of the refrigeration cycle. In refrigeration cycle, the heat exchanger of cold room outdoor unit is condenser, the heat exchanger of cold room indoor unit is evaporator. The refrigerant cycle is below:
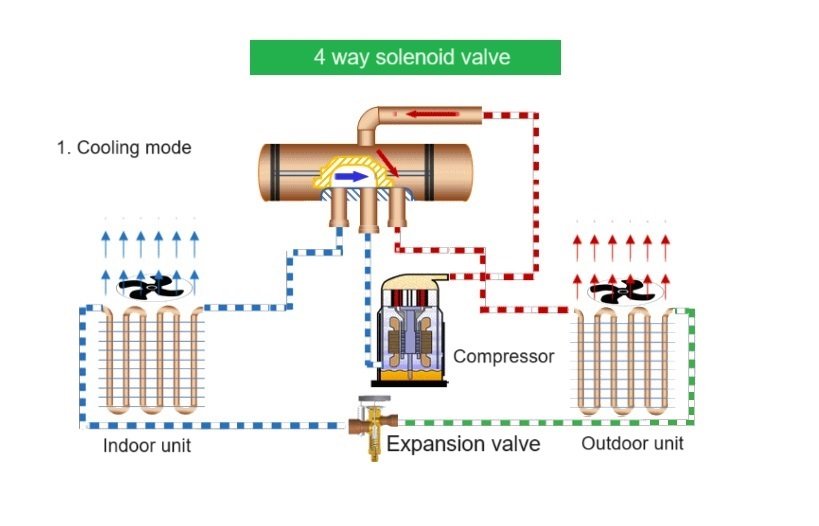
In hot gas defrost cycle, it uses a four-way to change the refrigerant flow direction, so the heat exchanger of the cold room outdoor unit acts as evaporator, while the heat exchanger of the cold room indoor unit acts as a condenser. The hot gas operation is below:
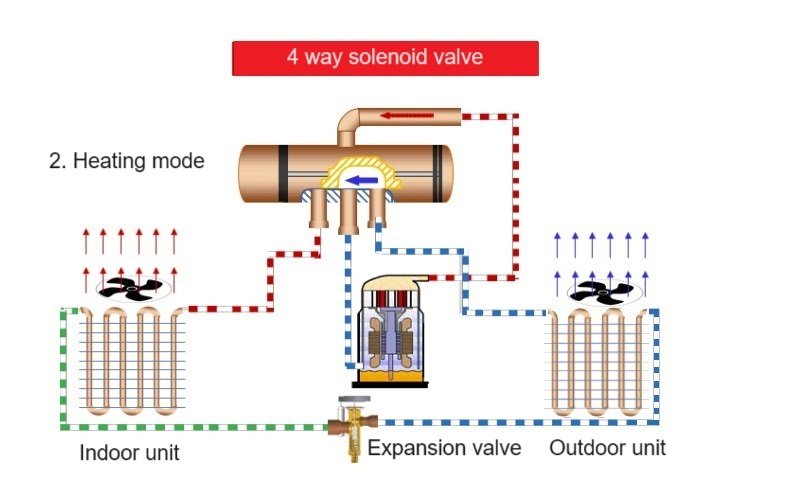
The superheated refrigerant vapor with a higher temperature is discharged from the compressor, flows to the evaporator directly. The evaporator is temporarily used as a condenser and the heat released to melt the frost layer on the evaporator surface.
Compared with electric defrost refrigeration system, the hot gas defrosting has many advantages.
Advantages of hot gas defrosting:
- Fast defrost efficiency
- Short defrost time
- High energy utilization efficiency
- Energy saving
- Small temperature fluctuations
Disadvantages of hot gas defrosting:
- Slightly higher initial investment
Hot gas defrost system for refrigeration systems, combines an optimized mechanical hot gas defrost system with today’s proven technology to provide the best solution to your needs. It greatly reduce the defrost energy consumption of refrigeration systems, and is the most economic defrosting methods in refrigeration, especially in medium and large refrigeration systems.
Hot gas defrost is the energy-efficient alternative to electric defrost refrigeration system. Glen Refrigeration offers ceiling mounted monoblock refrigeration unit, wall mounted monoblock refrigeration unit with reverse cycle defrost and hot gas defrost system (including split condensing unit and evaporator). Please click here for more information:
Wall Mounted Monoblock Refrigeration Unit

Suitable for small & medium cold rooms, freezer rooms, quick and easy installation.
Ceiling Mounted Monoblock Refrigeration Unit

Suitable for small & medium cold rooms, freezer rooms, quick and easy installation.
Are you interested in HOT GAS DEFROST REFRIGERATION SYSTEMS FOR COMMERCIAL REFRIGERATION?
For inquiries about the Hot Gas Defrost Refrigeration System, email us at info@greehvacr.com
Or feel free to call us at +86 15057108995
Or Whatsapp +86 15057108995
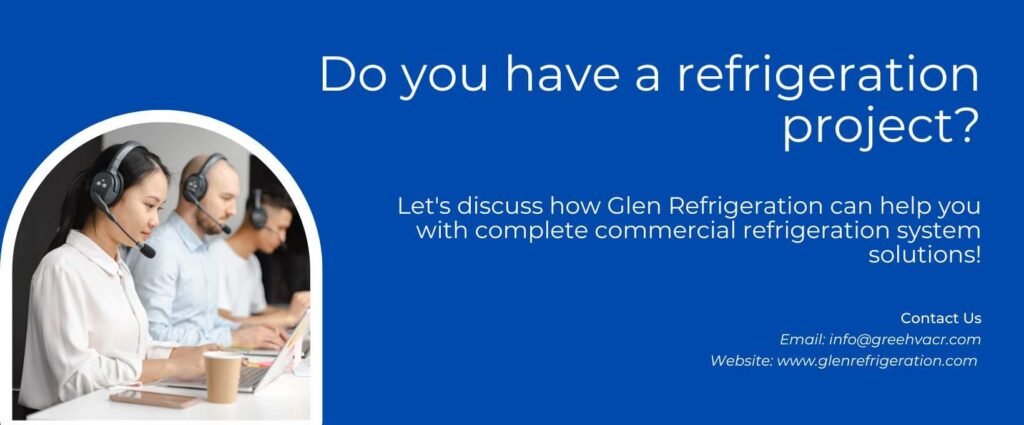